Table of Contents
3D printing, also known as additive manufacturing, is revolutionizing the manufacturing industry by transforming traditional production methods. This technology creates three-dimensional objects from digital models by adding material layer by layer, as opposed to traditional subtractive methods where material is removed from a solid block. The impact of 3D printing on manufacturing is profound, influencing design processes, production efficiency, supply chains, and product customization. This article explores how 3D printing is reshaping the manufacturing landscape, its benefits, and the challenges it faces.
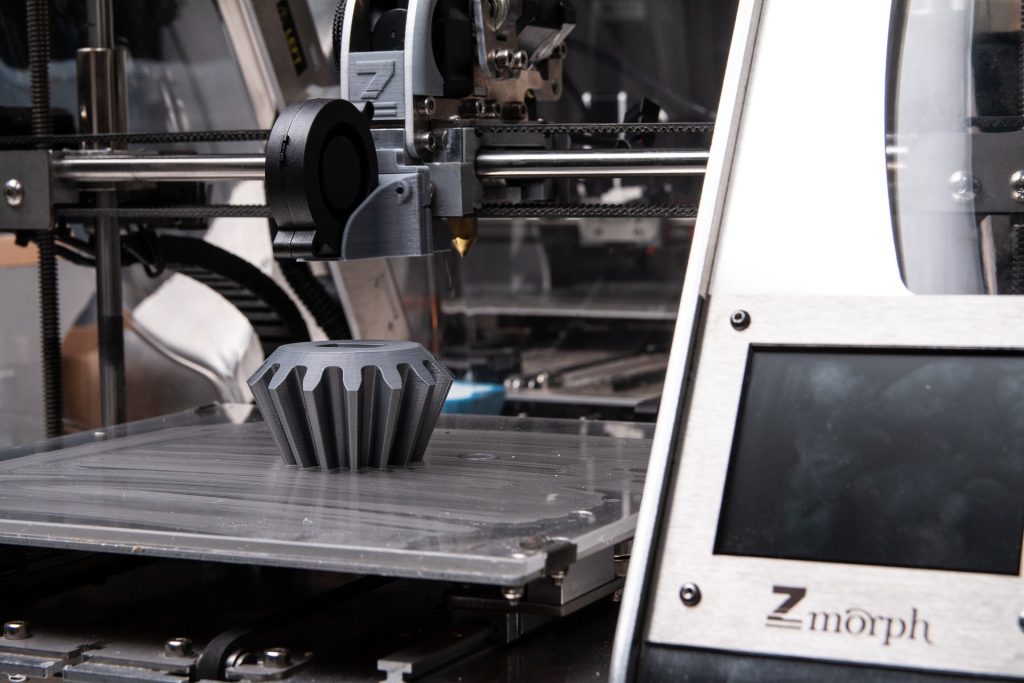
Benefits of 3D Printing in Manufacturing
- Design Flexibility and Innovation: 3D printing allows for greater design flexibility compared to traditional manufacturing methods. Designers and engineers can create complex geometries and intricate structures that would be difficult or impossible to achieve with conventional techniques. This freedom fosters innovation, enabling the development of novel products and solutions. For instance, in aerospace and automotive industries, 3D printing is used to design lightweight, optimized parts that enhance performance and fuel efficiency.
- Rapid Prototyping: One of the most significant advantages of 3D printing is its ability to accelerate prototyping. Traditional prototyping methods can be time-consuming and costly, requiring multiple iterations to refine a design. 3D printing streamlines this process by allowing rapid production of prototypes directly from digital designs. This speed enables faster testing and validation of concepts, reducing time-to-market and development costs.
- Cost Efficiency for Small-Batch Production: 3D printing is particularly advantageous for small-batch production runs. Traditional manufacturing often involves high setup costs for tooling and molds, making it economically unfeasible for low-volume production. With 3D printing, the cost of producing small quantities of parts or products is significantly reduced, as it does not require specialized tooling. This cost efficiency is beneficial for industries such as medical devices and custom consumer products.
- Customization and Personalization: 3D printing facilitates mass customization and personalization of products. By adjusting digital models, manufacturers can produce custom-designed items tailored to individual preferences or specific needs. In the healthcare sector, for example, 3D printing enables the creation of personalized implants and prosthetics that match a patient’s anatomy. Similarly, in consumer goods, products like custom jewelry or bespoke footwear can be designed and manufactured to individual specifications.
- Reduced Waste and Sustainable Manufacturing: Additive manufacturing is inherently more sustainable than traditional subtractive methods. Because 3D printing builds objects layer by layer, it uses only the necessary amount of material, reducing waste. Additionally, the ability to produce parts on demand and locally can minimize the need for transportation and large inventories, further reducing the environmental impact of manufacturing processes.
- Complex Supply Chains and Inventory Management: 3D printing can streamline supply chains and inventory management. By producing parts and products on-demand, manufacturers can reduce the need for extensive warehousing and inventory. This on-demand production capability allows for just-in-time manufacturing, which can enhance supply chain efficiency and responsiveness. Additionally, 3D printing can simplify the production of spare parts, which is particularly valuable for industries with complex machinery and equipment.
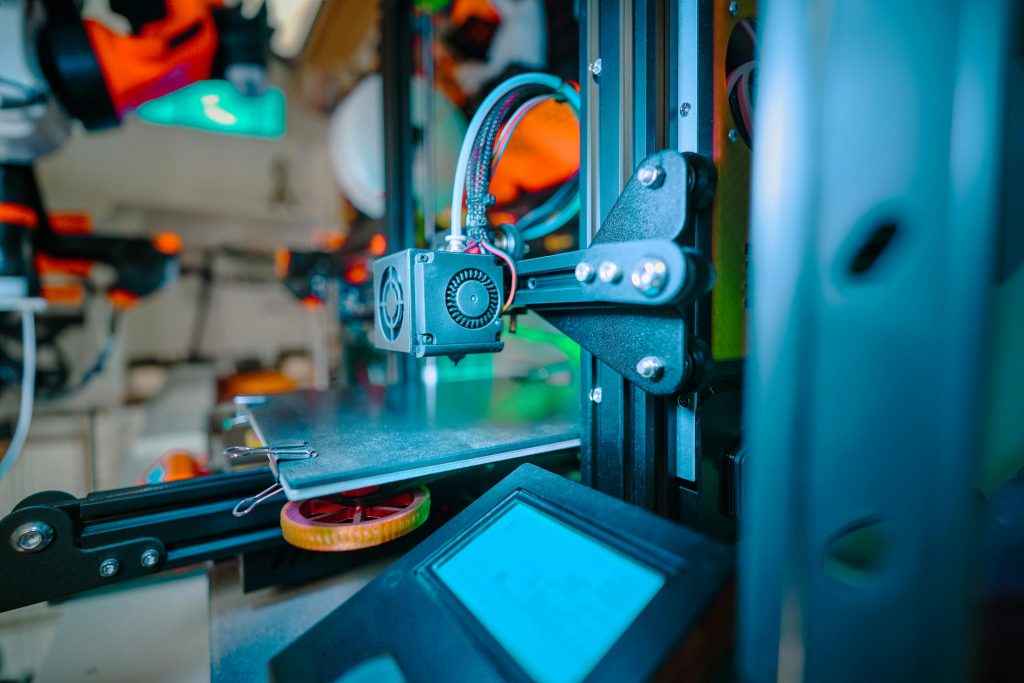
Applications of 3D Printing in Manufacturing
- Aerospace and Defense: In the aerospace and defense industries, 3D printing is used to produce lightweight, high-performance components. The technology enables the creation of complex geometries and optimized structures that contribute to improved fuel efficiency and reduced weight. Additionally, 3D printing is employed in rapid prototyping and production of custom parts for defense applications.
- Automotive: The automotive industry benefits from 3D printing through the production of prototypes, tooling, and custom parts. Manufacturers use 3D printing to design and test new components, such as engine parts and interior fittings. The technology also allows for the creation of custom-designed parts and low-volume production runs, enhancing design flexibility and innovation.
- Healthcare: In healthcare, 3D printing is revolutionizing the production of medical devices, implants, and prosthetics. Customized implants and prosthetics can be tailored to individual patients, improving fit and functionality. Additionally, 3D printing is used to create surgical guides and models for preoperative planning, enhancing surgical precision and outcomes.
- Consumer Goods: 3D printing enables the production of personalized consumer goods, such as custom jewelry, home decor, and fashion items. The ability to create unique, bespoke products on demand appeals to consumers seeking individuality and personalization. The technology also allows for rapid prototyping and small-batch production of new product designs.
- Architecture and Construction: In architecture and construction, 3D printing is used to create scale models, prototypes, and even full-scale building components. The technology allows architects and builders to explore innovative designs and construction methods. Additionally, 3D printing is being explored for creating affordable housing solutions and complex structural elements.
Challenges and Considerations
- Material Limitations: While 3D printing offers a range of materials, including plastics, metals, and ceramics, the selection is still limited compared to traditional manufacturing. Advances in material science are needed to expand the range of printable materials and improve the performance characteristics of 3D-printed parts.
- Speed and Scalability: Although 3D printing excels in rapid prototyping and small-batch production, it may not be as efficient for large-scale manufacturing compared to traditional methods. The speed of 3D printing can be slower than conventional production techniques, which can impact scalability for high-volume production runs.
- Quality and Consistency: Ensuring consistent quality and accuracy in 3D-printed parts can be challenging. Variations in printing conditions, material properties, and equipment calibration can affect the final product. Addressing these issues requires rigorous quality control and standardization processes.
- Intellectual Property and Design Protection: The digital nature of 3D printing raises concerns about intellectual property and design protection. Digital files used for 3D printing can be easily copied and shared, posing risks of unauthorized replication and counterfeiting. Manufacturers must implement measures to protect their designs and proprietary information.
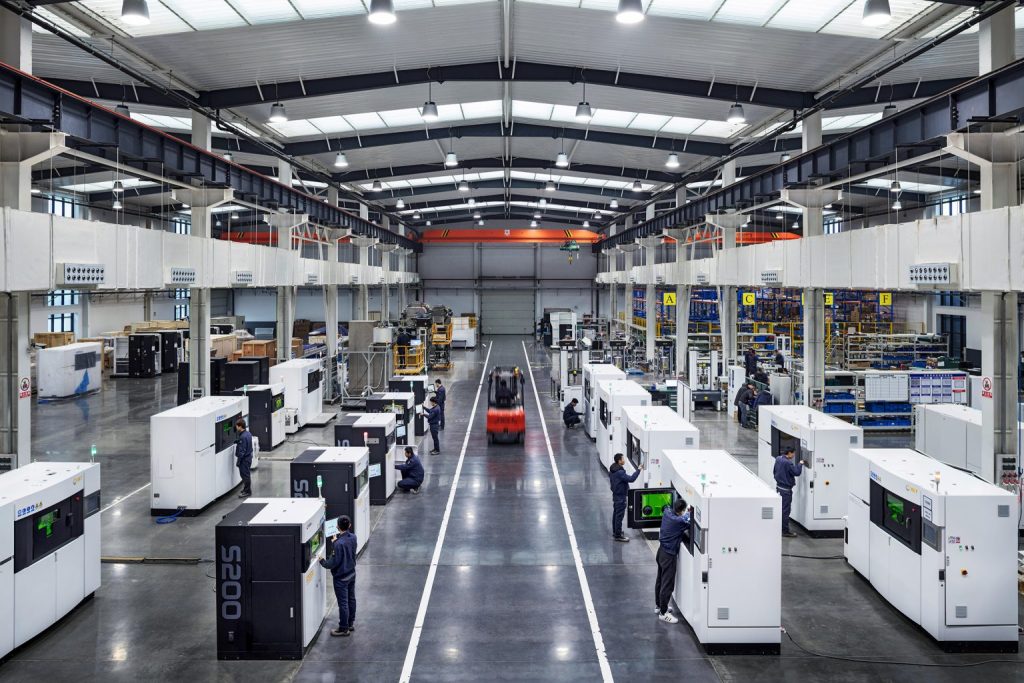
Conclusion
3D printing is transforming manufacturing by offering enhanced design flexibility, rapid prototyping, cost efficiency for small-batch production, and opportunities for customization. Its applications span various industries, including aerospace, automotive, healthcare, consumer goods, and construction. However, challenges such as material limitations, speed, quality consistency, and intellectual property protection must be addressed to fully realize the potential of 3D printing.
As technology continues to advance, 3D printing is likely to play an increasingly central role in manufacturing, driving innovation and efficiency. Embracing the benefits of additive manufacturing while addressing its challenges will be crucial for manufacturers seeking to leverage this transformative technology and stay competitive in a rapidly evolving industry.